Heat exchangers are among the most widely used devices in the process engineering industry. Until now, the design of heat exchangers was determined and limited by the available semi-finished products, such as tubes or stamped plates, and by the associated conventional manufacturing processes. Additive manufacturing now offers the opportunity to develop completely new and application-optimized apparatus concepts and heat exchanger types. Heat exchangers are also required in many high-pressure applications, where they have to withstand enormous operating pressures, which many conventional manufacturing processes can no longer guarantee.
Such high-pressure heat exchangers are required in hydrogen filling stations, for example. Depending on the tank system, maximum operating pressures of up to 875 bar occur during the refueling process in accordance with SAE standard J2601. At this pressure, the hydrogen must be cooled to a tank inlet temperature between -33°C and -40°C. To ensure this, a heat exchanger is required that can withstand this enormous operating pressure, provides the thermal output for all mass flows occurring during the refueling process and is also compact enough to be positioned in the installation space of the dispenser.
In cooperation with the IPeG and an industrial partner, this research project is developing a high-pressure minichannel heat exchanger made from 1.4404 using laser beam melting with a design pressure of 1050 bar. This can then be used in hydrogen filling stations, among other things, but the device should also be applicable and scalable for other high-pressure applications. Production using laser beam melting without joining represents a sensible alternative to other complex manufacturing processes with significantly greater geometric restrictions. The project includes the geometry determination, strength calculation using FEM simulations and, in the main part, the thermofluid-dynamic investigation using CFD simulations and experimental characterization to derive suitable correlations and models for apparatus design.
Supported by Investitions- und Förderbank Niedersachsen - NBank
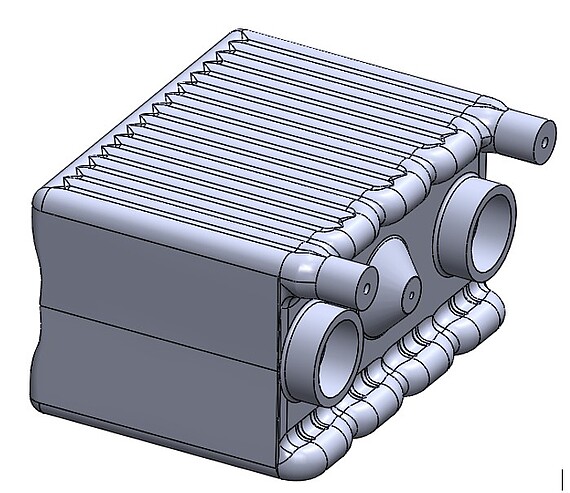
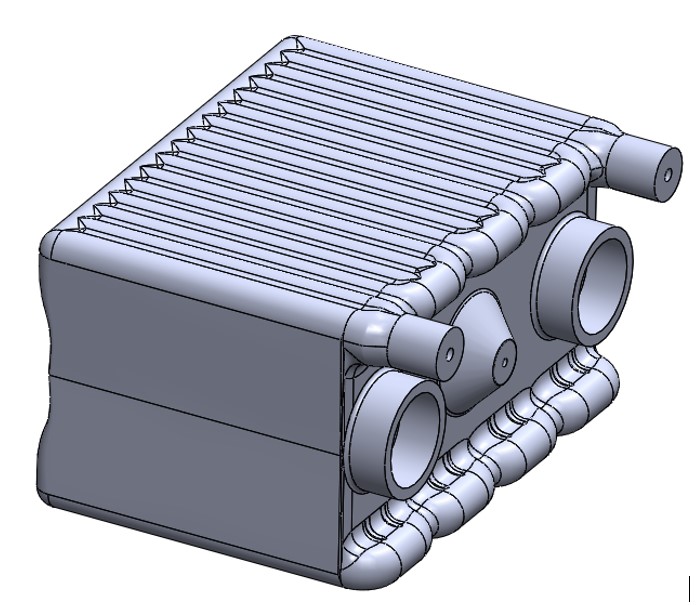
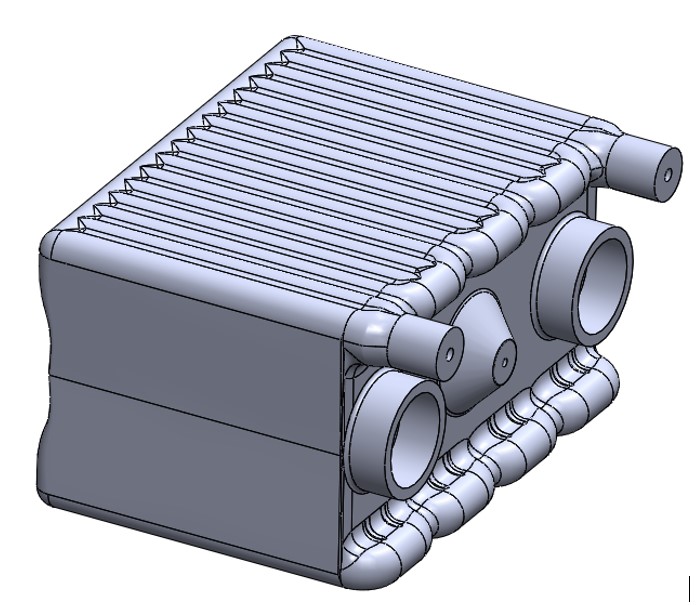


30823 Garbsen

